In the production of major household appliances like refrigerators, washing machines, and air conditioners, the TF-16 plays a crucial role. These appliances contain complex electrical systems with numerous connections. For instance, in refrigerators, the machine processes square-shaped wires ranging from 0.3 – 16mm² used for powering the compressor, controlling the internal lighting, and managing temperature sensors. Its precise stripping length adjustment (6 – 30mm) and accurate crimping ensure reliable electrical connections that can withstand vibrations and temperature fluctuations during the appliance’s operation. In washing machines, the TF-16 is utilized to crimp pre-insulated terminals on wires for motor controls, water inlet valves, and electronic control panels, enhancing the safety and durability of these connections.
For small electrical appliances such as electric kettles, toasters, and hair dryers, the TF-16’s versatility is highly valued. These devices require secure and efficient electrical connections within limited internal spaces. The machine’s ability to handle a wide range of wire sizes and its integrated functions, including vibration plate feeding and servo-driven crimping, enable quick and accurate terminal processing. For example, in electric kettle production, it ensures that the power cord connections are robust, preventing loose connections that could lead to electrical failures or safety hazards. The touchscreen operation allows for easy parameter adjustment, making it suitable for the production of various small appliance models.
In the production of smartphone and tablet chargers, the TF-16 is essential for creating reliable power connections. Chargers need to transmit electrical power safely and efficiently, and the machine’s precise crimping capabilities guarantee that pre-insulated terminals are securely attached to the wires. It processes the square-shaped wires commonly used in charger cables, ensuring that the insulation and conductivity are maintained. The automatic trigger start feature speeds up the production process, allowing manufacturers to meet the high demand for chargers. Additionally, the machine’s ability to save and recall parameter settings enables quick adaptation to different charger designs and specifications.
Laptop power adapters, which handle higher power loads, rely on the TF-16 for high-quality wire and terminal processing. The machine’s stable air supply (0.5 – 0.6Mpa) combined with servo-driven crimping provides consistent and strong crimping force, ensuring that the terminals can withstand the electrical currents involved. It processes the wires for components such as the transformer, rectifier, and output connectors in power adapters. The enclosed structure of the TF-16 protects the internal components from dust and debris, which is crucial in the clean production environments required for consumer electronics manufacturing, thus maintaining the quality and reliability of the power adapters.
Automotive wiring harnesses are intricate networks of wires that demand precise terminal crimping for reliable electrical performance. The TF-16 is employed to process the diverse wires in these harnesses, which connect components like the engine control unit, headlights, taillights, and interior electronics. Its capacity to handle wires from 0.3 – 16mm² makes it suitable for the wide range of wire gauges used in automotive applications. The machine’s accurate stripping and crimping functions ensure that the electrical connections are secure, reducing the risk of electrical failures caused by loose terminals. The hybrid electric-pneumatic design allows for flexibility in handling different terminal types and wire configurations commonly found in automotive wiring harnesses.
In the rapidly growing field of electric vehicles, the TF-16 is used for processing wires in critical components such as battery management systems, charging ports, and electric motor controllers. EVs have strict requirements for electrical connections due to high-voltage and high-current operations. The machine’s high-precision servo-driven crimping ensures that the pre-insulated terminals provide excellent electrical insulation and conductivity, enhancing the safety and performance of EV components. The compact size of the TF-16 allows for easy integration into EV production lines, where space is often limited, while its high production efficiency helps meet the increasing demand for EV components.
Industrial control panels, which serve as the central command centers for automated production lines, require reliable electrical connections. The TF-16 is used to process the wires for components within these panels, including relays, switches, and programmable logic controllers (PLCs). Its ability to handle different wire sizes and terminal specifications, along with the precise control over stripping and crimping, ensures that the electrical connections in control panels are stable and durable. The touchscreen operation and parameter-saving features enable quick setup for different control panel designs, reducing production time and increasing efficiency in industrial automation projects.
For industrial instrumentation and sensor systems, accurate wire and terminal processing is vital for reliable data transmission. The TF-16 processes the wires connected to instruments such as pressure gauges, flow meters, and temperature sensors. Its capacity to handle specific stripping lengths and terminal tube dimensions ensures that the electrical connections are optimized for the proper functioning of these devices. The machine’s high-quality crimping reduces the risk of signal interference and connection failures, which could lead to inaccurate measurements and system malfunctions. The safe and agile operation of the TF-16 makes it suitable for use in industrial environments where safety and precision are of utmost importance.
In the production of telecommunications network equipment, such as routers, switches, and network interface cards, the TF-16 is used to process the wires for internal power supplies and signal transmission circuits. These devices require stable and reliable electrical connections to ensure uninterrupted network operation. The machine’s precise crimping capabilities prevent electrical shorts and signal losses, enhancing the performance of network equipment. Its ability to handle a variety of wire sizes and terminal types makes it adaptable to the diverse wiring requirements in telecommunications equipment manufacturing. The automatic functions of the TF-16, such as vibration plate feeding and servo-driven crimping, improve production efficiency, allowing manufacturers to meet the high demand for network equipment.
Although fiber optic cables are the primary medium for data transmission in telecommunications, the associated electrical components in fiber optic terminal equipment still need reliable wire and terminal connections. The TF-16 is used to process the wires for powering and controlling these components. Its accurate stripping and crimping ensure that the electrical connections in fiber optic terminal equipment are secure, preventing power interruptions and signal degradation. The enclosed and compact design of the machine makes it suitable for installation in the limited spaces of telecommunications equipment production facilities, while its high production efficiency helps in the mass production of fiber optic terminal equipment.
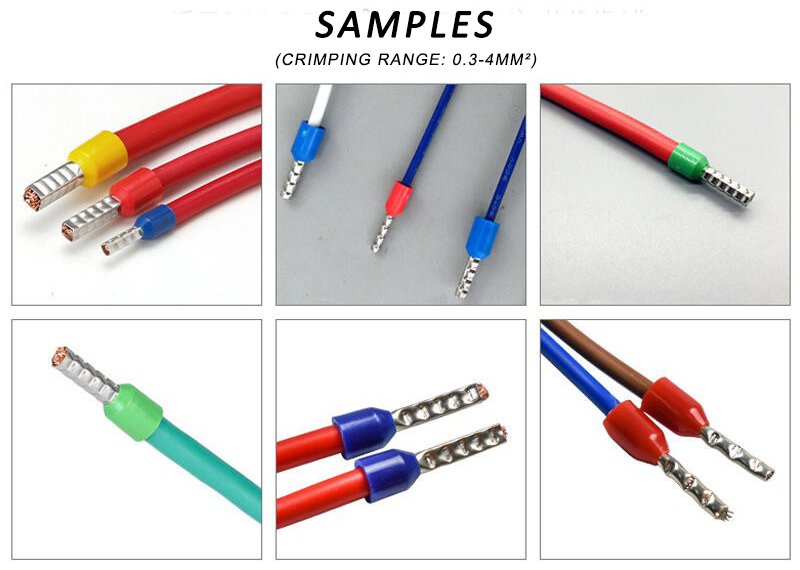